Atmospheric Plasma Treatment Prior To Selective Conformal Coating
- Brian Stumm
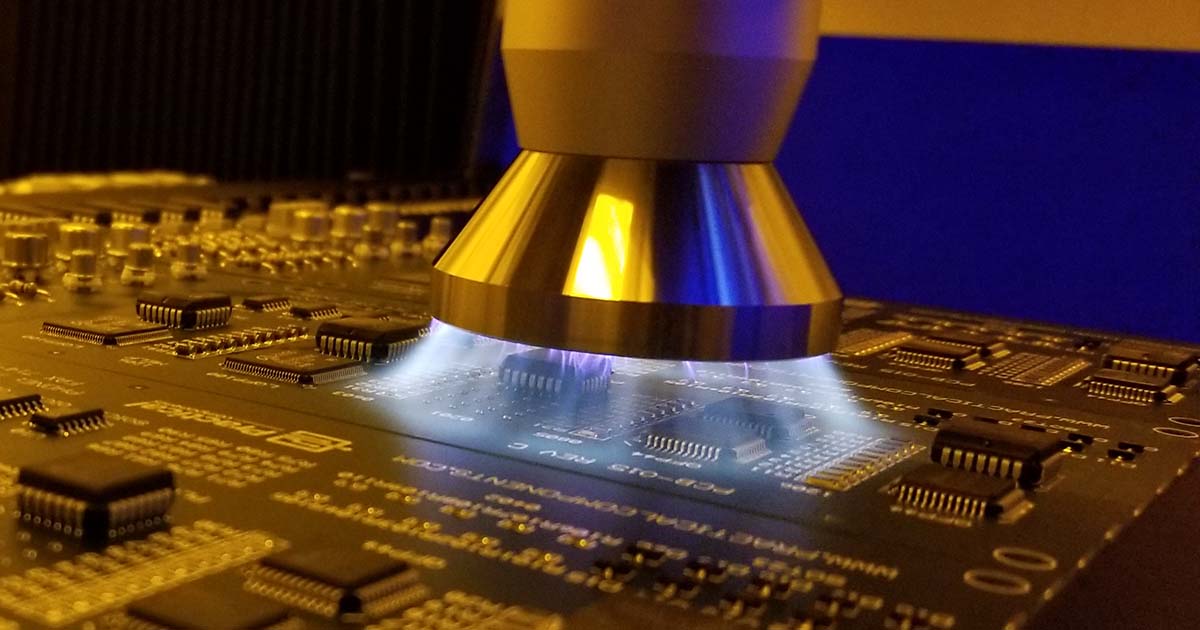
ABSTRACT
One of the most common causes of defects in the conformal coating process is contamination of the printed circuit assembly resulting in bubbles, dewetting or delamination of the cured coating material. The images below illustrate this contamination related defect.
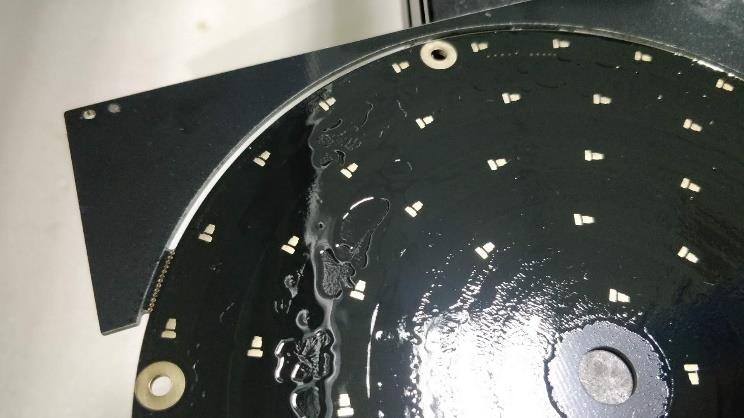
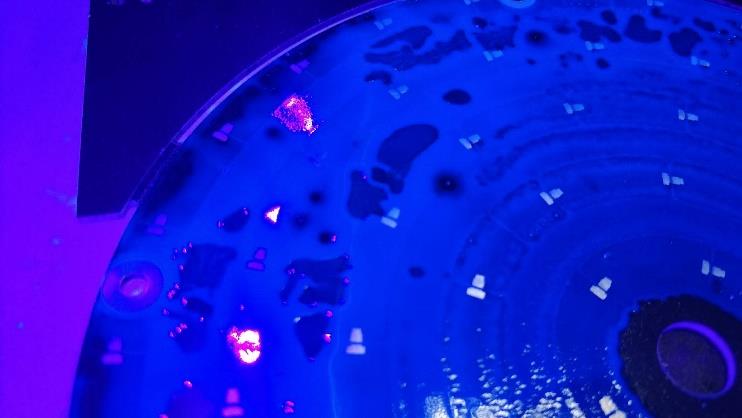
Plasma Treatment removes contaminants and increases surface energy, thus offering a potential solution to these common failures. Plasma Treatment is a form of surface modification. It is used in the pretreatment of material surfaces prior to gluing, bonding, painting, dispensing, or coating and can be used on virtually any material surface including those of textiles, metals, plastics, glass, etc.
Plasma is generated by combining a gas with an increased amount of energy where the gas becomes electronically charged with freely moving electrons in both the negative and positive state. This cocktail of neutral gas atoms, positive ions, UV light along with other excited gas molecules and atoms is packed with loads of internal energy. Plasma treatment is initiated when this energy comes into contact with the surface of a substrate.
There are two common forms of plasma treatment Low Pressure Plasma (Vacuum Plasma) and Atmospheric Plasma that are used for surface modifications of substrates. Vacuum Plasma is created using a vacuum pump in which most of the air is removed from a sealed chamber. With enough air removed, the chamber low-pressure reaches adequate levels for ionizing the remaining air or gases with a strong electrical field producing plasma. All surfaces of a material are treated at the same time using Vacuum Plasma. Atmospheric Plasma on the other hand requires no closed chamber, it is produced by electrically energizing air or gases as they pass through a nozzle at surrounding atmosphere or normal pressure using a pulsed electric arc generated by high voltage discharge.
The effects of plasma treatment are short lived, typically allowing less than one hour to apply coatings or adhesives. Atmospheric Plasma Treatment allows for in-line processing, eliminating the time constraint and the need for labor intensive, batch processing. The purpose of this study is to confirm the feasibility of in-line, atmospheric plasma treatment prior to automated, selective conformal coating of printed circuit boards.
Read more, click to download white paper
This white paper was presented during the SMTA International Expo (Chicago, IL) on September 22nd, 2019.